by Luminis Health
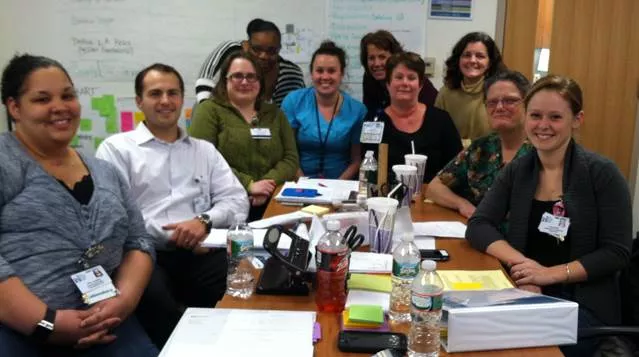
There have been a lot of amazing changes happening in the Laboratory lately. The group has been working diligently to improve workflow and efficiency in one of the busiest areas of the hospital. Accuracy and efficiency are hugely important—almost every patient who passes through our doors will need to use lab services before they are discharged. More than 3,000 specimens pass through the lab on any given day, and the team needs to be able to process them quickly and accurately. Making their workflow as efficient as possible will keep costs low for patients. It will also put results in the hands or their caregivers quicker, helping them make faster, more accurate care decisions for their patients.
One of the improvements the team recently made is in their workflow once a specimen enters the lab. They recently participated in a week-long rapid improvement event (RIE) to reduce the amount of time it took for a specimen to begin to be tested once it was received as well as reduce errors and decrease costs.
Specimens arrive in the lab through the tube system, via delivery or drop-off. Once received, the lab assistants receiving the specimen must determine where the specimen needs to go for testing and, if necessary, prepare the specimen. This receiving and dispersal area is known as Central Accessioning.
The first step was to take a closer look at the work area. The team determined that the Central Accessioning station was cluttered and not effectively used. The set-up of the station forced the lab assistants to make multiple stops in several areas within the workstation before finally delivering the specimen to the testing station. Extra walking means extra time.
The team worked to redesign the workflow and eliminated the need to use the majority of the Central Accessioning station. The accessioning team can complete all work in a clean central location. This new centralized workstation means that instead of walking in a scattered “spaghetti” pattern, the Central Accessioning team walks “the bat cape.” The bat cape pattern represents the standardized walking pattern of receiving and delivering specimens to testing.
The team saw results immediately, including:
- A cleaner space: The team was able to remove cubicle walls which were made unnecessary in the revamped accessioning station, giving the space a cleaner, more open feel and allowing for a more efficient walking pattern.
- Quicker processing: On average, a specimen would spend more than 16 minutes in accessioning before moving on to testing. That’s been reduced to less than seven minutes.
- Increased specimen processing: Each employee can now process more than 600 specimens per day, up from 424 before the rapid improvement event (RIE).
- Elimination in overtime: The team was putting in an additional 2.4 hours before the RIE.
- Decrease in errors: Before the RIE, six specimens processed incorrectly. Now, that’s down to four.